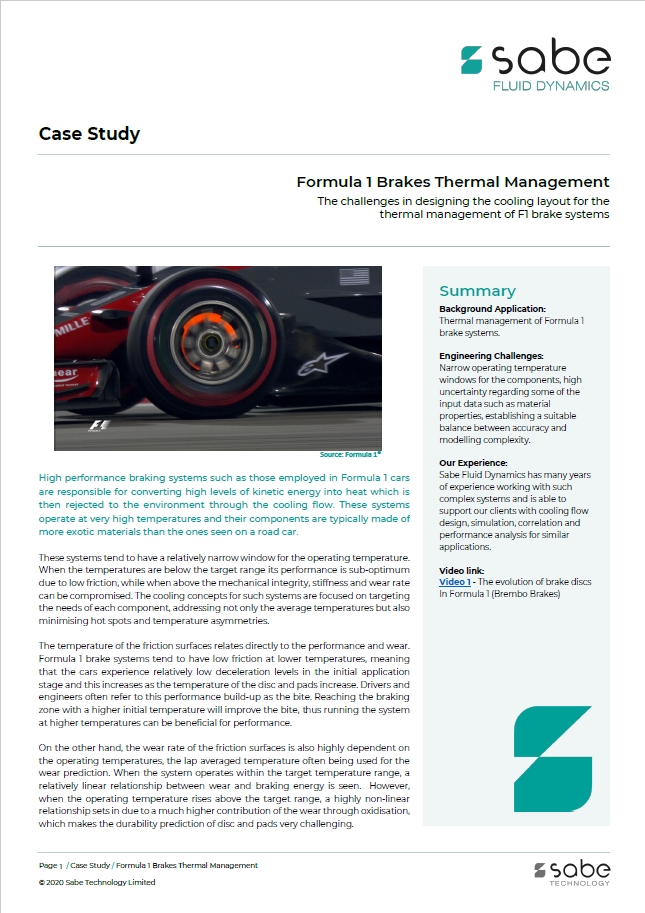
Background Application:
Thermal management of Formula 1 brake systems.
Engineering Challenge:
Narrow operating temperature windows for the components, high uncertainty regarding some of the input data such as material properties, establishing a suitable balance between accuracy and modelling complexity.
Our Experience:
Sabe Fluid Dynamics has many years of experience working with such complex systems and is able to support our clients with cooling flow design, simulation, correlation and performance analysis for similar applications.
Video Link:
Video 1 – The evolution of brake discs In Formula 1 (Brembo Brakes)
High performance braking systems such as those employed in Formula 1 cars are responsible for converting high levels of kinetic energy into heat which is then rejected to the environment through the cooling flow. These systems operate at very high temperatures and their components are typically made of more exotic materials than the ones seen on a road car.
These systems tend to have a relatively narrow window for the operating temperature. When the temperatures are below the target range its performance is sub-optimum due to low friction, while when above the mechanical integrity, stiffness and wear rate can be compromised. The cooling concepts for such systems are focused on targeting the needs of each component, addressing not only the average temperatures but also minimising hot spots and temperature asymmetries.
The temperature of the friction surfaces relates directly to the performance and wear. Formula 1 brake systems tend to have low friction at lower temperatures, meaning that the cars experience relatively low deceleration levels in the initial application stage and this increases as the temperature of the disc and pads increase. Drivers and engineers often refer to this performance build-up as the bite. Reaching the braking zone with a higher initial temperature will improve the bite, thus running the system at higher temperatures can be beneficial for performance.
On the other hand, the wear rate of the friction surfaces is also highly dependent on the operating temperatures, the lap averaged temperature often being used for the wear prediction. When the system operates within the target temperature range, a relatively linear relationship between wear and braking energy is seen. However, when the operating temperature rises above the target range, a highly non-linear relationship sets in due to a much higher contribution of the wear through oxidisation, which makes the durability prediction of disc and pads very challenging.
Formula 1 carbon disc brakes are tested to destruction to establish the minimum operating thickness and this limit is used as reference by the trackside engineers to estimate the components’ life in terms of number of laps at a given wear rate. In extreme cases the driver might be told to employ “lift and coast” to reduce the operating temperatures and bring the wear rate under control, such technique relies on the driver lifting off the throttle several meters before the braking zone to make use of the aerodynamic drag for some of the initial deceleration.
The system operating temperature will also influence the mechanical properties of the materials, which can be relevant for structural components such as the upright and calipers. High average or localised temperatures can result in a reduction of the structural stiffness of the component, which will in turn affect the system’s response time. Within the caliper itself, hot spots could also cause the hydraulic fluid temperature to raise above its boiling point which will translate into a sudden increase in the fluid compressibility and a very detrimental effect on the system’s response characteristics, the driver will describe the instance as a “soft pedal”.
A final thermal management challenge worth mentioning is the use of the braking thermal energy or its cooling capacity to affect the temperature of the rims and tyres, which adds another dimension to the cooling design. This technique is widely used in Formula 1 to encourage the tyres to operate within a desired temperature window, sometimes aiming at overall grip, sometimes front/rear balance or in some other instances in an attempt to prolong the tyre life during a race stint.
From the modelling perspective, such complex systems offer yet many other challenges. The quality of the input data is often compromised by relatively high levels of uncertainty regarding material properties, this is related to the difficulties associated to their measurements at such high temperatures in controlled environments. Carbon discs have anisotropic thermal conductivity which tends to be dependent on the manufacturing method and can vary significantly from part to part.
Another modelling difficulty is establishing a suitable level of complexity to the model. A too complex model which includes most of the conduction and radiation paths, mesh movement and transient thermal loads can quickly grow into an impractical model for development. While such level of complexity would almost certainly translate into a high level of modelling accuracy, some of the added accuracy would likely be within the noise created by the uncertainty within the input data. In a competitive environment like Formula 1, unnecessary complexity means increased use of resources and, more importantly, increased turnaround time for development iterations which will return a slower development rate and a performance cost associated to it.
Sabe Fluid Dynamics has many years of experience working with the above-mentioned aspects of these complex systems. We are able to support our clients with cooling flow design, simulation, correlation and performance analysis for this and similar applications. Contact us to discuss your challenge!
Sabe Technology Ltd | +44 (0) 1327 221427 | [email protected]